4 million hours without a lost-time incident
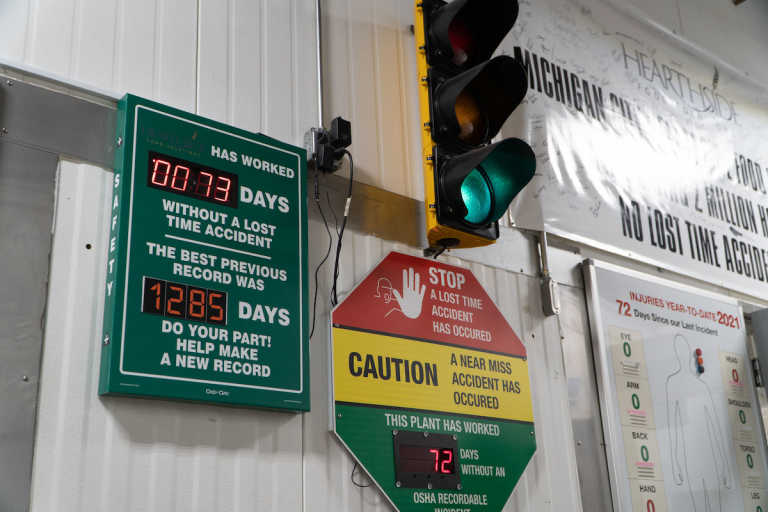
Jan 01, 2020
The challenge
A strong stance on safety is table stakes in manufacturing. Without it, nothing else works. Of course, that doesn’t mean it comes easy. Keeping our people safe each and every day is an ongoing challenge that requires constant vigilance.
Though there are many ways to quantify safety, making it to the one million hour mark without a lost-time incident is considered a huge accomplishment across the industry. This landmark is also one that many plants struggle to reach. With so many details to track, daily labor demands, and sheer number of employees, it’s easy to see how sizable this challenge can be.
Not to mention, many plants also fall into a reactive state when it comes to safety instead of taking full stock of preventative measures. When you feel like you’re constantly putting out little fires, it’s difficult to find the time and space for preventative planning.
The process
From the beginning, we set out to make the safety of our people our number one priority. We know that a successful company is proactive (rather than reactive), and have taken steps to weave it into our culture and day-to-day activities.
To us, safety means that every employee gets to start, work, and finish safe each day. We enact this by creating safety committees at each plant made up of hourly employees who are engaged and empowered in their daily work with safety as a focus. These safety teams are the eyes and ears of the floor, and help to:
- Identify risks and hazards
- Create a safe and healthy environment on a daily basis
- Engage all employees, inviting them in to be part of the process, identify risks, near misses, and collaborate on solutions
These committees have proved invaluable when it comes to the cultivation of a strong overall culture of safety. Because the hourly employees on these teams are the ones communicating and pushing safety initiatives, they have been able to positively influence overall buy-in from the ground up.
With their help, we’ve been able to take an engaging, lighthearted approach to this serious requirement. From a safety phrase of the week, to prizes for safety accomplishments on the floor, to instituting a “safety t-shirt Tuesday” tradition, we do our best to keep things fun, while still focusing on serious work.
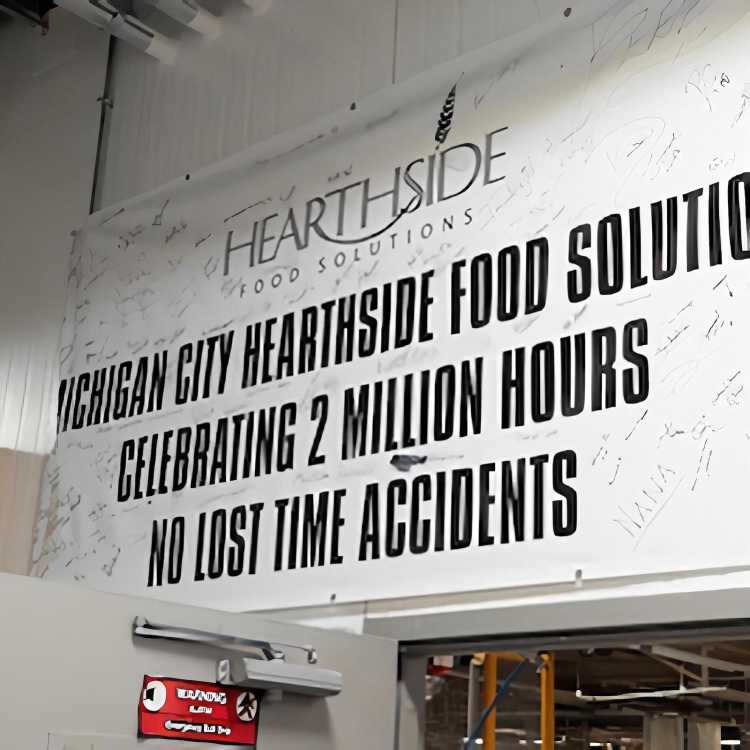
The results
We’re proud of the work toward safety that all of our plants take, but one plant in particular stands out as the first Hearthside facility to not only surpass the one million hour mark...but to carry it through to four million hours without a lost-time safety incident. This is an incredible point of pride for not only this particular plant, but for the company as a whole. And, they haven’t stopped there–this plant is currently pushing to get to five million hours. We give credit where it’s due, and threw this plant a party to acknowledge and thank them for all of their hard work.
Additionally, their positive influence on other plants has been incredible to watch. They set the bar higher, which has ignited other teams to strive for big milestones.
When we prioritize safety as a company, we’re putting our people first. Being a safe and reliable workplace has a rich trickle-down effect. It not only keeps our employees protected, but also allows them to continue to support their families. A culture of safety also improves the quality of the products we make, and gives our customers peace of mind in the processes that we take to manage their products.