Using data effectively to advance manufacturing practices
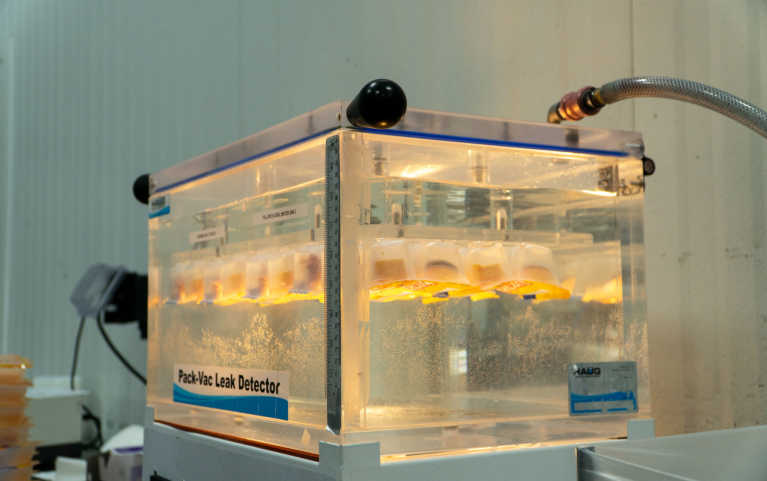
May 01, 2020
Our mission
Goals on every metric. Swift to address red flags. We’re constantly asking ourselves: how can we be better?
When it comes to manufacturing, the Hearthside Performance System (HPS) is our “secret” to success. This system is fine-tuned to continuously monitor and improve plant performance by leaning into data, identifying issues quickly, and taking swift action when needed. We’ve identified key metrics that are tracked diligently every shift, day, and in some circumstances, even every hour. If the goal for each metric is being met, it’s identified as green. If it’s not, the metric is immediately flagged as red.
This seemingly simple red-versus-green identification system helps us quickly isolate and respond to complex abnormalities. Our management team is able to rely on the HPS to stay on top of any issues while permanently addressing the root of the problem to ensure that it doesn’t reoccur.
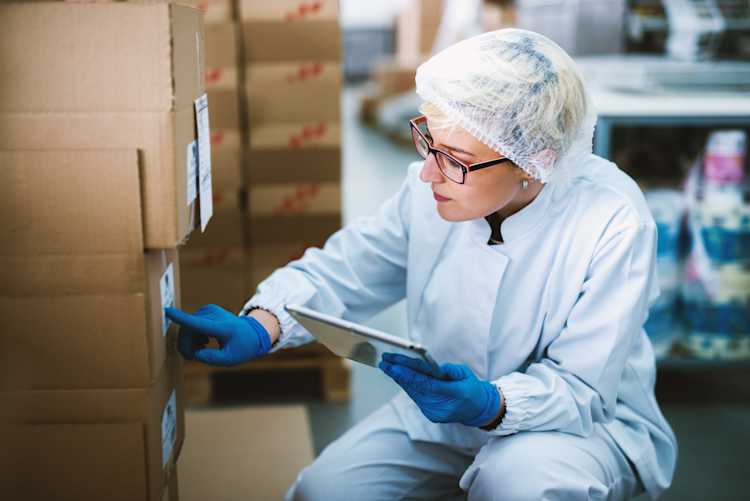
Overcoming key challenges
Many of our plants operate with sizable employee bases of over 1,000 people...essentially the size of a small village. Getting this level of manpower aligned, bought in, and operating smoothly as a team is no small task. Yet, it’s essential to maintain the upstanding quality and scale with which Hearthside operates.
We rise to this challenge by prioritizing our people. We believe that a community is a group of people who agree to grow together, and we enact this value through empowerment at every job level. At Hearthside, everyone has a career plan or path within the company if they demonstrate initiative, ability, and motivation. We empower employees by giving them the lean tools to be solution-oriented to the problems that they encounter day-to-day. This gives them some skin in the game, purpose, and a greater sense of pride in their job. When employees feel empowered, job satisfaction, quality of work, and consistency all improve.
Triumphs
Mistakes happen and problems arise, but our performance system has given us the ability to respond with impressive speed. The data that we get from the HPS helps us remove opinions and any potential bias in order to get to the root cause of problems—and actually solve them. It keeps us measured and honest: two vital values when measuring manufacturing success.
Additionally, our onboarding process and employee development gives us a leg up, long-term. We want to give each person the tools to control their own destiny, and envision what their future with the company could look like. That starts with their first day on the job.
Simply put, when we have enough of the right people, everything else falls into place. When you invest in your people, you invest in the company.